The “Make in India” program was launched by Prime Minister Narendra Modi on 25 September 2014. Since then, from within the 25 targeted sectors, the Defence Manufacturing sector has received a very quick and positive response due to various complimentary policy measures. The government must now move ahead and also fast track the program in other service as well as manufacturing sectors, which may not necessarily be classified as under Defence, yet hold immense strategic significance for the economy, as well as the security of the nation in terms of cost and criticality. The nature of the products and services may, more often than not, have a dual or multiple end use and effect, and contribute towards building a robust and well diversified industrial base; so necessary to achieve self sufficiency in weapon systems. These sectors are:-
- Electronic System and Design and Manufacturing (ESDM) Sector to manufacture silicon chips, the most basic and essential building blocks for manufacturing electronic hardware products for various applications.
- Heavy and precision engineering units capable of manufacturing finished products such as aero engines, airframe structures from composite materials, high strength steel and alloy structures, high performance diesel and gas turbine engines as also transmission systems including their components and LRUs.
- Companies capable of becoming systems integrators by compounding technologies such as IT, Digital, Electronics and Mechanical to churn out smart Control Systems for commercial as well as defence applications, such as Power Grid Management, Air Traffic Control and Network Centric Battle Field Surveillance, Control, Decision and Management Systems for land sea, air and aerospace.
- Maintenance, Repair and Overhaul (MRO) facilities for military and civil aircraft for the domestic and foreign market.
- IT companies in the field of development of application software.
While there are many industrial sectors engaged in the field of dual use technology, three sectors stand out for the sheer scale of current and future demand and criticality of their products, in context to national security as well as the nation’s economic well being, i.e. Electronics, Aerospace and Shipbuilding.
Electronics Industry
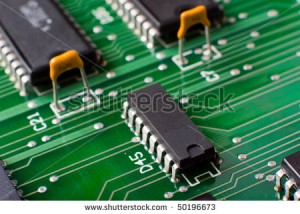
The National Policy on Electronics 2012 had assessed that by the year 2020, the cost of India’s electronics import may far exceed the cost of oil imports. This fact goes unnoticed because electronics, as a “meta resource” forms a significant component of all machines and equipment, which are classified in their final sectoral forms, e.g., automobiles, aviation, health equipment, media and broadcasting, defence armaments, etc. Setting up of fabrication plants to indigenously manufacture silicon chips was the only recommended solution. Fabrication plants for manufacture of silicon chips have to be built to stringent environmental requirements, they are highly capital intensive and also require a large amount of land and water.
Two consortia – led by HSMC Technologies India and Jaiprakash Associates were given in-principle approval in 2013 to set up one plant each. It was estimated that an investment of more than Rs 60,000 crore, would be required for these two projects, the government had agreed to subsidise forty percent of the investment. As of December 2015 there has been no progress mainly due to the two consortia being unable to raise their share of the financial investment. It takes approximately three years to set up a plant and thereafter commence manufacture. The government will have to find a way out and get the road blocks removed.
Indigenous Aerospace Industry
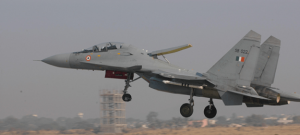
Hindustan Aeronautics Limited (HAL) is the sole producer of aircraft, mainly military, that to with a very small manufacturing capacity. It also manufactures jet engines for the Sukhoi 30 MKI and Jaguar fighters and the Shakti turbo shaft engine for the Advanced Light Helicopter Dhruv under licence from Russia, UK and France respectively. The Kaveri engine designed and developed by GTRE for the LCA, at a cost of Rs 2101 crore has not been successful even after more than 25 years since sanctioning of its development.
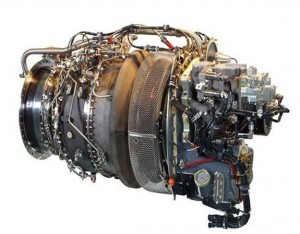
The situation obtaining in 2015 is much different from that when the Kaveri project was sanctioned in 1989. India has attained self sufficiency in various types of high grade Titanium alloys from the vast ore deposits in the country. Coupled with this, capability for manufacturing engine parts like turbine fans and engine cores through casting and forging Titanium alloys has also been achieved for the Kaveri, as also through import substitution for licence built Russian and UK engines. HAL and Bharat Forge Ltd are already exporters of Titanium components as part of a global supply chain of components for Rolls Royce and Airbus.
Further, India has the fourth largest air force and is assessed to be the third largest aviation and aero space market by 2020, with an airlines fleet of over 800 passenger jet aircraft. It is a matter of grave concern and financial drain that a meagre 5-10% of the MRO work for domestic scheduled carriers is being carried out in India. The rest are being outsourced abroad. It therefore makes economic sense to set up MROs within the country to meet the requirements of the domestic airlines.
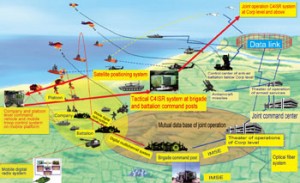
If India aspires to be a great power, it is indeed an imperative that India must build its own aero engines for the bulk of its civil and military aircraft. The size of the military and civilian aviation market presents a great opportunity to India; it must be used to strengthen the base of the domestic aerospace industry, by creating an enabling environment for its rapid growth through the following measures:-
- Leverage offsets towards manufacture and export of aerospace components by Indian Industry to major global aerospace companies for civil and military aircraft.
- Leverage offsets to set up MROs for aero engines for commercial and military aircraft and helicopters in service and for likely future acquisitions.
- Create competition for HAL, the sole aircraft manufacturer, by incentivising private sector industries to enter aerospace manufacturing. Besides diversification of manufacturing centres, this will also lead to increase in indigenous manufacturing capacity for commercial as well as military aircraft.
- Design and develop an engine for the Regional Transport Aircraft (RTA) which could also at a later date meet the requirements of powering a military Medium Transport Aircraft (MTA).
- Design and develop a turbo shaft engine to power the commercial versions of the future Light Utility Helicopter.
- Build on the lessons and realised technologies of the Kaveri engine to develop a family of engines for various types of indigenous commercial and military aircraft.
Shipbuilding
India’s merchant shipping fleet ranks 16th in the world in terms of gross tonnage. Approximately, 95 percent of the country’s total trade by volume and 70 percent by value is undertaken by using ships. However, only 10.9 percent of the shipments are carried by Indian Ships, resulting in a payout of US $ 57 billion to foreign shipping firms. To prevent this drain, besides other policy measures, India also needs to build up its merchant fleet. Indian shipping industry is mostly sourcing ships through imports. In 2014, India was ranked at the 11th position in Ship Building with a market share of only 0.6% in the world shipbuilding industry. Ironically, out of the 28 shipyards in the country, the five under the Ministry of Defence are facing a glut of orders from the Indian Navy and the Coast Guard, which they cannot fulfil in the required timeframe, while most of the 20 shipyards in the private sector are under severe financial stress due to lack of adequate orders. Realising the neglect of the shipbuilding industry the government on 18 December 2015, has announced a new policy for shipbuilding which has gone the whole hog in announcing generous incentives and financial support to achieve a 5% share of the global shipbuilding market by 2020.
There is a need for looking at both commercial ship building and warship building in tandem so as to reap the enormous opportunities which can flow out of such initiatives. Countries like South Korea and China have become global powers in ship building due to focused government attention, liberal policy and investment in infrastructure and design capability. A vibrant domestic ship building industry will also catalyse the growth of other sectors such as the steel sector and the engineering industries manufacturing various types of marine diesel and gas turbine engines. Offsets against defence purchases from foreign sources must be ploughed back in modernising shipyards in adapting to modular building techniques and establishing manufacturing capability for propulsion systems.
(Disclaimer: The views and opinions expressed in this article are those of the author and do not necessarily reflect the official policy or position of BharatShakti.in)